Rather by definition, embedded software involves building a gizmo of some sort. Manufacturing the hardware portion of the gizmo turns out to be somewhat more complicated than writing a Makefile and starting the build... who knew?
Today, Gentle Reader, we'll discuss the realities of building hardware products by meandering through a few topics:
- Contract Manufacturing
- Distributors
- Contract Engineering
- DVT and Compliance
Contract Manufacturing

Contract manufacturers build a product according to a completed design including the Bill of Materials, the layout of the printed circuit board, assembly instructions, system tests, etc. They can do as much or as little as desired, from a single board up to a completed and tested system directly shipped to your customer.
In the last 25 years contract manufacturing has essentially taken over the production of all electronic goods. The economies of scale from producing such large volumes are overwhelming, and there are very few companies who maintain their own production facilities now. The capital expenses for kitting out an assembly line are daunting, the CM can amortize the cost over a huge number of products. Some well known contract manufacturing firms are Foxconn (also known as Hon Hai), Flextronics (which owns Solectron, another large CM), Celestica, and Sanmina-SCI.
Contract Manufacturers thrive on volume. If building something in really small volumes it is worth looking into production shops aimed at hobbyists, such ExpressPCB.
One thing to keep firmly in mind: the value of a customer to a CM is measured entirely by the volume of future business they expect. If order volumes drop off, the CM will rapidly lose interest. If your market suffers a serious downturn you may find that the quality of the product drops precipitously as the CM rushes through the build in order to get to another, more profitable customer. Similarly if you decide to terminate business with a CM and move to a competing firm, expect astonishingly bad build quality on the final order.
Distributors
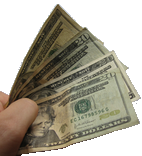
Like it or not, distributors are absolutely necessary in the embedded market. There are tens of thousands of customers buying millions of components. The component manufacturers simply cannot afford to maintain individual relationships with each customer when a distributor can represent multiple manufacturers with the same effort and expense.
Many Distributors provide FAEs (Field Application Engineers) to assist their customers in selecting components. A good FAE is extremely valuable, due to the sheer number of product designs they have been involved in. They will often be able to suggest alternatives which you might not otherwise have found, and know which parts have been problematic in other designs.
Distributors and RegistrationDistributors who perform a significant amount of technical support during the design of a product cannot allow themselves to be undercut by a cheaper alternative in production. Therefore the component manufacturers allow distributors to register as being responsible for the design win at a particular customer. Only that distributor will be allowed to offer advantageous pricing, other distributors will not be allowed to undercut them.
Distributors do a lot more business with the big Contract Manufacturers than any individual customer, and CMs value their relationship with the distributor more than any individual customer. It is not unknown for a Distie to legitimately claim the design win for one particular component, then obtain the Bill of Materials from the CM and register themselves for every chip in the design. Choosing a Distributor is much like getting married: be very certain that the relationship will work in the long term before signing on the dotted line.
Contract Engineering
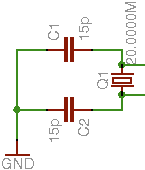
For a niche market with well-defined needs, a product can sell for years with minimal changes. In these cases its better to contract out the design than recruit a team. The contract will include the functional spec to be designed, timelines for completion, etc. The engineering firm will supply the requisite hardware, software, and firmware expertise, and the resulting design will belong to the customer.
Alternately, Contract Engineering firms can fill in gaps for an in-house design team. For example after components have been chosen and the design competed, a layout for the printed circuit board must be created. A good layout of a complex PCB requires an experienced designer and expensive CAD tools. It makes no sense to keep such a person on staff if only a few designs are done each year, so it is often contracted out. Mechanical design of the chassis and other sheet metal is also often done outside, for the same reason.
Contracts in this area are essentially always on a time and materials basis. The upfront estimate of total cost is not guaranteed. Fixed price contracts are exceedingly rare, because they represent an enormous risk to the engineering firm if the design time goes over estimates. In most cases this will work out fine: the engineering firm will want to get the design done quickly in order to move on to the next customer. However if business slows, watch out for unjustified padding of billable hours.
Design Verification Test

Not every unit coming out of the factory will be identical. Each component in the design has a tolerance, an allowed deviation which is still considered within specification. Every system coming off the line will contain parts slightly above spec or below, and it is important to insure that the complete system will still function reliably even if it contains components at the extreme ends of the tolerance. Though the hardware design takes these tolerances into account, in the real world it is difficult to anticipate every possible interaction of components and PCBs.
This is where DVT, for Design Verification test, comes in. During DVT the hardware engineers measure the system to ensure it not only does what it is supposed to do, but does so with sufficient margin to handle variances in its components. DVT is time-consuming work, and changes are often made in the production system based on what is found in the prototypes.
Compliance

The ubiquitous Underwriters Laboratories logo is likely the most widely known example of a compliance certification, but it is not the only one. There are a huge number of standards for product safety or performance, some recognized around the globe and others specific to each geographic market.
Some industries place much more stringent requirements on their products than others. For example, the NEBS Level 3 guidelines for the telecommunications market specifies that there be no noxious chemicals released if the equipment catches fire.
Conclusions
One of the aims of this blog is to provide insight into fields of software development which don't get as much exposure as Ruby on Rails or web frameworks. I've tried to provide an overview of some of the gritty details of building products. Its really quite exciting when the first prototype of a new system comes back from the factory, and you try to boot the software for the first time. When it doesn't boot, reality hits.
I'd like to thank John Walsh for much feedback and good suggestions of topics to cover in this posting.